Si bien es solo una parte de un sistema mucho más grande, la punta de contacto en las pistolas de soldadura por arco metálico con gas (GMAW), tanto robóticas como semiautomáticas, desempeña un papel fundamental a la hora de proporcionar una buena calidad de soldadura. También puede influir de manera mensurable en la productividad y rentabilidad de su operación de soldadura: el tiempo de inactividad por cambios excesivos puede ser perjudicial para el rendimiento y el costo de la mano de obra y el inventario.
Las funciones principales de una punta de contacto son guiar el alambre de soldadura y transferir la corriente de soldadura al alambre a medida que pasa a través del orificio. El objetivo es que el alambre pase a través de la punta de contacto suavemente, manteniendo al mismo tiempo el máximo contacto. Para obtener los mejores resultados, es importante utilizar el tamaño de punta de contacto (o diámetro interior (ID)) correcto para la aplicación. Tanto el alambre de soldadura como el proceso de soldadura influyen en la selección (Figura 1).
Impacto del alambre de soldadura en el tamaño de la punta de contacto
Tres características del alambre de soldadura afectan directamente la selección de la punta de contacto para una aplicación particular:
▪ Tipo de cable
▪ Alambre fundido
▪ Calidad del cable
Tipo-Los fabricantes de puntas de contacto suelen recomendar puntas de contacto de tamaño estándar (predeterminado) para los cables correspondientes, como una punta de contacto xxx-xx-45 para cables de 0,045 pulgadas. En algunos casos, sin embargo, puede ser preferible sobredimensionar o sobredimensionar la punta de contacto según el diámetro del alambre.
Las tolerancias estándar de los alambres de soldadura varían según el tipo. Por ejemplo, el código 5.18 de la American Welding Society (AWS) permite ± 0,001 pulgadas. Tolerancia de 0,045 pulgadas. cables sólidos y ± 0,002 pulg. Tolerancia de 0,045 pulgadas. alambres tubulares. Los alambres tubulares y de aluminio, que son blandos, funcionan mejor con puntas de contacto estándar o de gran tamaño que les permiten pasar con una fuerza de alimentación mínima y sin pandearse ni torcerse dentro del alimentador o la pistola de soldar.
Los cables macizos, por el contrario, son mucho más rígidos, lo que significa menos problemas de alimentación, lo que permite combinarlos con puntas de contacto de tamaño insuficiente.
Elenco-La razón para sobredimensionar o subdimensionar la punta de contacto se relaciona no sólo con el tipo de alambre, sino también con su forma y hélice. El molde se refiere al diámetro del bucle de alambre cuando se ha dispensado un trozo de alambre del paquete y se ha colocado sobre una superficie plana; esencialmente, la curvatura del alambre. El umbral típico para el yeso es de 40 a 45 pulgadas; Si el molde del alambre es más pequeño que esto, no utilice una punta de contacto de tamaño inferior.
La hélice se refiere a cuánto se eleva el cable desde esa superficie plana y no debe ser superior a 1 pulgada en ningún lugar.
AWS establece requisitos para el alambre fundido y la hélice como control de calidad para garantizar que el alambre disponible se alimente de una manera que conduzca a un buen rendimiento de la soldadura.
Una forma aproximada de obtener la cantidad total de alambre fundido es por el tamaño del paquete. El alambre empaquetado en paquetes a granel, como un tambor o carrete, puede mantener un molde más grande o un contorno más recto que el alambre empaquetado en carrete o bobina.
El "alambre recto" es un punto de venta común para los alambres empaquetados a granel, ya que es más fácil alimentar alambre recto que alambre curvo. Algunos fabricantes también tuercen el cable mientras lo empaquetan en el tambor, lo que hace que el cable forme una onda sinusoidal en lugar de un bucle cuando se saca del paquete. Estos cables tienen un molde muy grande (100 pulgadas o más) y se pueden combinar con puntas de contacto de tamaño inferior.
Sin embargo, el alambre alimentado desde un carrete más pequeño tiende a tener un molde más pronunciado: aproximadamente 30 pulgadas. o menor, y normalmente requiere un tamaño de punta de contacto estándar o mayor para proporcionar las características de alimentación adecuadas.
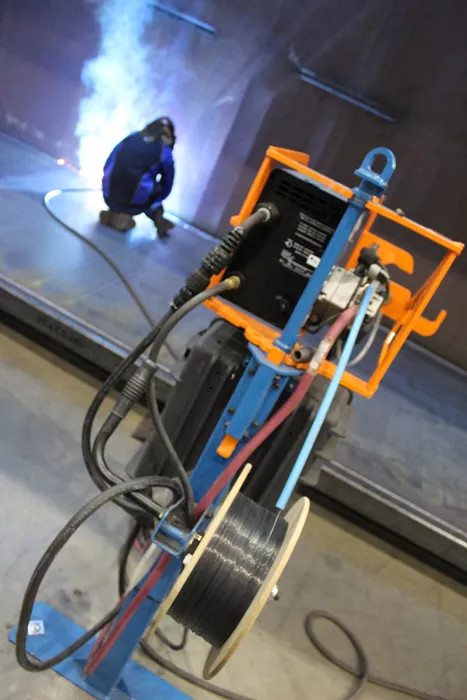
Figura 1
Para obtener los mejores resultados de soldadura, es importante tener el tamaño de punta de contacto adecuado para la aplicación. Tanto el alambre de soldadura como el proceso de soldadura influyen en la selección.
Calidad-La calidad del cable también afecta la selección de la punta de contacto. Las mejoras en el control de calidad han hecho que el diámetro exterior (OD) de los alambres de soldadura sea más preciso que en años anteriores, por lo que se alimentan con mayor suavidad. El alambre macizo de alta calidad, por ejemplo, ofrece un diámetro y una fundición constantes, así como un revestimiento de cobre uniforme en la superficie; Este cable se puede utilizar junto con una punta de contacto que tiene un diámetro interior más pequeño, porque hay menos preocupación por que el cable se doble o se doble. El alambre tubular de alta calidad ofrece los mismos beneficios, junto con costuras suaves y seguras que evitan que el alambre se abra durante la alimentación.
El alambre de mala calidad que no se fabrica según estándares estrictos puede ser propenso a una mala alimentación del alambre y a un arco errático. No se recomienda el uso de puntas de contacto de tamaño insuficiente con cables que tengan amplias variaciones de diámetro exterior.
Como precaución, siempre que cambie a un tipo o marca de cable diferente, es importante volver a evaluar el tamaño de la punta de contacto para asegurarse de lograr los resultados deseados.
Efecto del proceso de soldadura
En los últimos años, los cambios en las industrias de fabricación y fabricación han impulsado cambios en el proceso de soldadura, así como en el tamaño de la punta de contacto que se utilizará. Por ejemplo, en la industria automotriz, donde los fabricantes de equipos originales utilizan materiales más delgados (y más resistentes) para ayudar a reducir el peso del vehículo y mejorar la eficiencia del combustible, los fabricantes suelen utilizar fuentes de energía con formas de onda avanzadas, como cortocircuitos pulsados o modificados. Estas formas de onda avanzadas ayudan a reducir las salpicaduras y aumentar la velocidad de soldadura. Este tipo de soldadura, típicamente empleada en aplicaciones de soldadura robótica, es menos tolerante a las desviaciones en el proceso y requiere puntas de contacto que puedan entregar la forma de onda de manera precisa y confiable al alambre de soldadura.
En un proceso típico de soldadura por pulsos que utiliza 0,045 pulgadas. En un cable sólido, la corriente máxima puede ser superior a 550 amperios y la velocidad de aumento de corriente puede ser superior a 1 ´ 106 amperios/seg. Como resultado, la interfaz de punta de contacto a cable funciona como un interruptor a la frecuencia de pulso, que es de 150 a 200 Hz.
La vida útil de la punta de contacto en la soldadura por pulsos suele ser una fracción de la de la soldadura GMAW o de voltaje constante (CV). Se recomienda seleccionar una punta de contacto con un ID ligeramente más pequeño para el cable que se está utilizando para garantizar que la resistencia de la interfaz entre la punta y el cable sea lo suficientemente baja como para que no se produzcan arcos drásticos. Por ejemplo, un cable sólido de 0,045 pulgadas de diámetro combinaría bien con una punta de contacto con un diámetro interior de 0,049 a 0,050 pulgadas.
Las aplicaciones de soldadura manual o semiautomática requieren consideraciones diferentes a la hora de seleccionar el tamaño de punta de contacto adecuado. Las pistolas de soldar semiautomáticas suelen ser mucho más largas y tener contornos más complicados que las pistolas robóticas. A menudo también hay una mayor curvatura en el cuello, lo que permite al soldador acceder cómodamente a la junta soldada. Un cuello con un gran ángulo de flexión crea un molde más apretado en el alambre a medida que se introduce. Por lo tanto, es una buena idea seleccionar una punta de contacto con un diámetro interior ligeramente mayor para permitir una alimentación suave del alambre. En realidad, esta es la clasificación tradicional de tamaños de puntas de contacto. La mayoría de los fabricantes de pistolas de soldar establecen el tamaño de punta de contacto predeterminado según la aplicación semiautomática. Por ejemplo, un 0,045 pulgadas. El alambre sólido de diámetro coincidiría con una punta de contacto con un DI de 0,052 a 0,055 pulgadas.
Consecuencias del tamaño incorrecto de la punta de contacto
El tamaño incorrecto de la punta de contacto, ya sea demasiado grande o demasiado pequeña para el tipo, fundición y calidad del alambre que se utiliza, puede provocar una alimentación errática del alambre o un rendimiento deficiente del arco. Más específicamente, las puntas de contacto con diámetros internos demasiado pequeños pueden hacer que el cable se enganche dentro del orificio, lo que provoca una quemadura (Figura 2). También puede provocar la formación de nidos de pájaros, que es una maraña de alambre en los rodillos impulsores del alimentador de alambre.
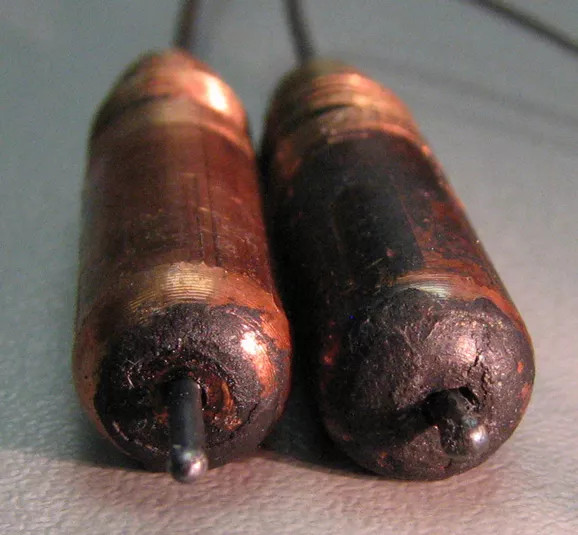
Figura 2
Burnback (cable atascado) es uno de los modos de falla más comunes de las puntas de contacto. Se ve significativamente afectado por el diámetro interior (ID) de la punta de contacto.
Por el contrario, las puntas de contacto con un diámetro interior demasiado grande para el diámetro del cable pueden permitir que el cable se desvíe mientras pasa. Esta desviación resulta en una pobre estabilidad del arco, fuertes salpicaduras, fusión incompleta y desalineación de la soldadura en la unión. Estos sucesos son especialmente significativos en la soldadura por impulsos agresiva; La tasa de desgaste (tasa de desgaste) de ojo de cerradura (Figura 3) de una punta de contacto de gran tamaño puede ser el doble que la de una punta de contacto de tamaño pequeño.
Otras consideraciones
Es importante comprender completamente el proceso de soldadura antes de seleccionar el tamaño de la punta de contacto para el trabajo. Tenga en cuenta que la tercera función de la punta de contacto es actuar como fusible del sistema de soldadura. Cualquier problema en el tren motriz del circuito de soldadura se muestra (y debe mostrarse) primero como falla de la punta de contacto. Si la punta de contacto falla de manera diferente o prematura en una celda en comparación con el resto de la planta, es probable que esa celda necesite un ajuste fino.
También es una buena idea evaluar la tolerancia de su operación al riesgo; es decir, cuánto cuesta cuando falla una punta de contacto. En una aplicación semiautomática, por ejemplo, es probable que el operador de soldadura pueda identificar rápidamente cualquier problema y reemplazar una punta de contacto defectuosa de manera económica. Sin embargo, el costo por falla inesperada de la punta de contacto en una operación de soldadura robótica es mucho mayor que en la soldadura manual. En este caso, necesita sugerencias de contacto que funcionen de manera confiable durante el período entre cambios programados de sugerencias de contacto, por ejemplo, un turno. Generalmente es cierto que en la mayoría de las operaciones de soldadura robótica, la consistencia de la calidad proporcionada por una punta de contacto es más importante que su duración.
Tenga en cuenta que estas son sólo reglas generales para seleccionar el tamaño de la punta de contacto. Para determinar el tamaño correcto, es importante inspeccionar las puntas de contacto defectuosas en la planta. Si la mayoría de las puntas de contacto fallidas tienen un cable atascado en su interior, el ID de la punta de contacto es demasiado pequeño.
Si la mayoría de las puntas de contacto fallidas no tienen cables, pero se ha observado un arco irregular y una mala calidad de la soldadura, puede ser beneficioso seleccionar puntas de contacto de tamaño insuficiente.
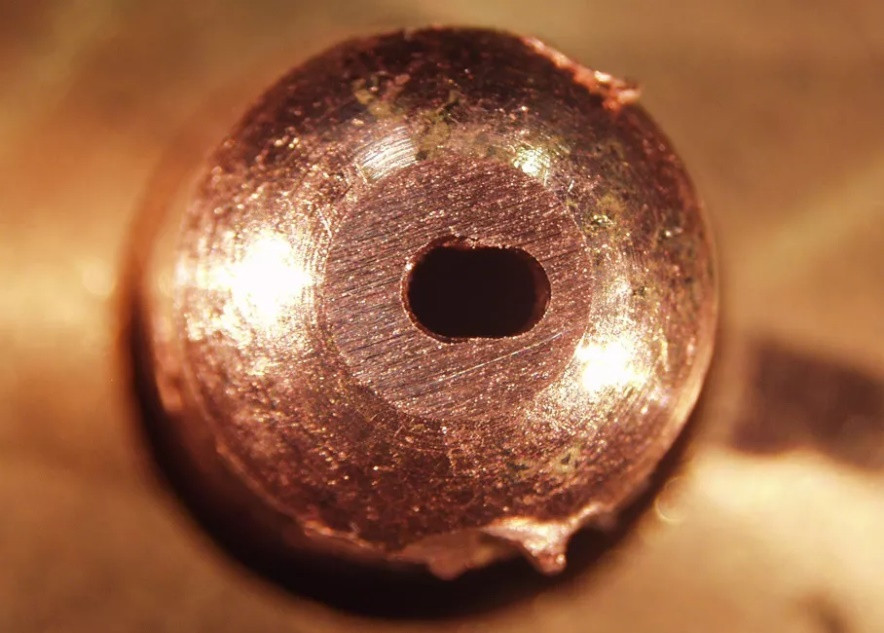
Figura 3
El ojo de cerradura excesivo también es uno de los modos de falla más comunes de las puntas de contacto. También se ve afectado significativamente por el diámetro interior (ID) de la punta de contacto.
Hora de publicación: 02-ene-2023