En aplicaciones de soldadura MIG, es fundamental tener una ruta de alimentación de alambre suave. El alambre de soldadura debe poder alimentarse fácilmente desde el carrete del alimentador a través de la clavija de alimentación, el revestimiento y la pistola y hasta la punta de contacto para establecer el arco. Esto permite al operador de soldadura mantener niveles constantes de productividad y lograr una buena calidad de soldadura, al mismo tiempo que minimiza el costoso tiempo de inactividad para la resolución de problemas y posibles retrabajos.
Sin embargo, existen varios problemas que pueden interrumpir la alimentación del alambre. Estos pueden causar una serie de problemas, incluido un arco errático, quemaduras (la formación de una soldadura en o sobre la punta de contacto) y nidos de pájaros (una maraña de cables en los rodillos impulsores). Para los nuevos operadores de soldadura que quizás no estén tan familiarizados con el proceso de soldadura MIG, estos problemas pueden resultar especialmente frustrantes. Afortunadamente, existen pasos para prevenir problemas fácilmente y crear una ruta de alimentación de alambre confiable.
La longitud del revestimiento de soldadura tiene un gran impacto en qué tan bien se alimentará el alambre a lo largo de todo el recorrido. Un revestimiento demasiado largo puede provocar torceduras y una mala alimentación del alambre, mientras que un revestimiento demasiado corto no proporcionará suficiente soporte al alambre a medida que pasa. En última instancia, esto puede provocar microarcos dentro de la punta de contacto que provocan quemaduras o fallas prematuras de los consumibles. También puede ser la causa de un arco errático y de anidación de pájaros.
Recorte el liner correctamente y utilice el sistema adecuado
Desafortunadamente, los problemas de recorte del revestimiento de soldadura son comunes, particularmente entre operadores de soldadura con menos experiencia. Para eliminar las conjeturas al recortar correctamente el revestimiento de una pistola de soldar y lograr una trayectoria de alimentación de alambre impecable, considere un sistema que elimine la necesidad de medir el revestimiento para reemplazarlo. Este sistema bloquea el revestimiento en su lugar en la parte posterior de la pistola, lo que permite al operador de soldadura recortarlo al ras con el pasador de alimentación. El otro extremo del revestimiento se bloquea en la parte delantera de la pistola en la punta de contacto; está alineado concéntricamente entre los dos puntos, por lo que el revestimiento no se extenderá ni se contraerá durante los movimientos de rutina.
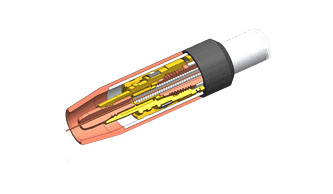
Un sistema que bloquea el revestimiento en su lugar en la parte posterior de la pistola y en la parte delantera proporciona una ruta de alimentación de alambre suave, a lo largo del cuello hasta los consumibles y la soldadura, como se ilustra aquí.
Cuando utilice un revestimiento convencional, evite torcer la pistola al recortar el revestimiento y utilice un medidor de recorte de revestimiento cuando se proporcione. Los revestimientos con un perfil interior que imparte menos fricción al alambre de soldadura a medida que pasa a través del revestimiento son una buena opción para lograr una alimentación de alambre eficiente. Estos tienen un revestimiento especial y están enrollados a partir de un material de perfil más grande, lo que hace que el revestimiento sea más resistente y ofrece una alimentación suave.
Utilice la punta de contacto adecuada e instálela correctamente
Hacer coincidir el tamaño de la punta de contacto de soldadura con el diámetro del alambre es otra forma de mantener una ruta de alimentación despejada. Por ejemplo, un cable de 0,035 pulgadas debe coincidir con la punta de contacto del mismo diámetro. En algunos casos, puede ser deseable reducir la punta de contacto en un tamaño para obtener una mejor alimentación del alambre y control del arco. Solicite recomendaciones a un fabricante de consumibles de soldadura o a un distribuidor de soldadura de confianza.
Busque desgaste en forma de orificios (cuando el orificio de la punta de contacto se desgasta y se vuelve oblongo), ya que esto puede causar un retroceso que impida que el cable se alimente.
Asegúrese de instalar la punta de contacto correctamente, apretándola con los dedos para evitar el sobrecalentamiento de la punta, lo que puede dificultar la alimentación del cable. Consulte el manual de operaciones del fabricante de la punta de contacto de soldadura para conocer la especificación de torque recomendada.
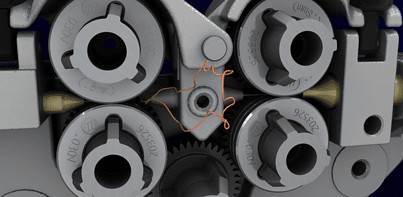
Un revestimiento mal recortado puede provocar nidos de pájaros o una maraña de alambre en los rodillos impulsores, como se ilustra aquí.
Elija los rodillos impulsores adecuados y ajuste la tensión correctamente
Los rodillos impulsores desempeñan un papel importante a la hora de garantizar que una pistola de soldar MIG tenga una trayectoria de alimentación de alambre suave.
El tamaño del rodillo impulsor debe coincidir con el tamaño del cable que se utiliza y el estilo depende del tipo de cable. Al soldar con alambre macizo, un rodillo impulsor con ranura en V favorece una buena alimentación. Los alambres con núcleo fundente (tanto con protección de gas como autoprotegidos) y los alambres con núcleo metálico funcionan bien con rodillos impulsores moleteados en V. Para soldar aluminio, utilice rodillos impulsores con ranura en U; Los alambres de aluminio son muy suaves, por lo que este estilo no los aplastará ni estropeará.
Para ajustar la tensión del rodillo impulsor, gire la perilla del alimentador de alambre media vuelta más allá del deslizamiento. Aprieta el gatillo de la pistola MIG, pasa el cable por una mano enguantada y dóblalo lentamente. El alambre debe poder avanzar sin deslizarse.
Comprender el impacto del alambre de soldadura en la alimentabilidad
La calidad del alambre de soldadura y el tipo de embalaje en el que se encuentra afectan la alimentación del alambre. El alambre de alta calidad tiende a tener un diámetro más consistente que los de baja calidad, lo que facilita su alimentación por todo el sistema. También tiene un molde consistente (el diámetro cuando se corta un trozo de alambre del carrete y se coloca sobre una superficie plana) y una hélice (la distancia que el alambre se eleva desde la superficie plana), lo que aumenta la alimentabilidad del alambre.
Si bien el alambre de mayor calidad puede costar más al principio, puede ayudar a reducir los costos a largo plazo al minimizar el riesgo de problemas de alimentación.
Inspeccione la punta de contacto para ver si hay agujeros en forma de cerradura, ya que puede provocar quemaduras (la formación de una soldadura dentro o sobre la punta de contacto), como se muestra en esta ilustración.
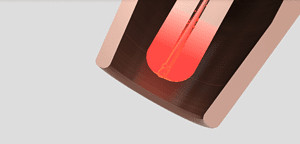
Los alambres de tambores grandes generalmente tienen un molde grande cuando se dispensan desde el empaque, por lo que tienden a alimentarse más rectos que los alambres de un carrete. Si el volumen de la operación de soldadura puede soportar un tambor más grande, esto puede ser una consideración tanto para fines de alimentación de alambre como para reducir el tiempo de inactividad para el cambio.
Haciendo la inversión
Además de seguir las mejores prácticas para establecer una ruta clara de alimentación de alambre y saber cómo solucionar problemas rápidamente, es importante contar con equipos confiables. La inversión inicial en un alimentador de alambre de alta calidad y consumibles de soldadura duraderos puede dar sus frutos a largo plazo al reducir los problemas y los costos asociados con los problemas de alimentación del alambre. Menos tiempo de inactividad significa más concentración en producir piezas y entregarlas a los clientes.
Hora de publicación: 14-mar-2017