La porosidad, discontinuidades de tipo cavidad formadas por el atrapamiento de gas durante la solidificación, es un defecto común pero engorroso en la soldadura MIG y tiene varias causas. Puede aparecer en aplicaciones semiautomáticas o robóticas y requiere eliminación y reelaboración en ambos casos, lo que genera tiempo de inactividad y mayores costos.
La principal causa de la porosidad en la soldadura de acero es el nitrógeno (N2), que interviene en el baño de soldadura. Cuando la piscina de líquido se enfría, la solubilidad del N2 se reduce significativamente y el N2 sale del acero fundido, formando burbujas (poros). En la soldadura galvanizada/galvanneal, el zinc evaporado se puede agregar al baño de soldadura y, si no hay tiempo suficiente para escapar antes de que el baño se solidifique, forma porosidad. Para la soldadura de aluminio, toda la porosidad es causada por hidrógeno (H2), de la misma manera que funciona el N2 en el acero.
La porosidad de la soldadura puede aparecer externa o internamente (a menudo llamada porosidad subsuperficial). También puede desarrollarse en un solo punto de la soldadura o en toda su longitud, lo que resulta en soldaduras débiles.
Saber cómo identificar algunas causas clave de la porosidad y cómo resolverlas rápidamente puede ayudar a mejorar la calidad, la productividad y el resultado final.
Mala cobertura de gas de protección
La mala cobertura del gas de protección es la causa más común de la porosidad de la soldadura, ya que permite que los gases atmosféricos (N2 y H2) contaminen el baño de soldadura. La falta de cobertura adecuada puede ocurrir por varias razones, que incluyen, entre otras, una tasa de flujo de gas de protección deficiente, fugas en el canal de gas o demasiado flujo de aire en la celda de soldadura. Las velocidades de desplazamiento demasiado rápidas también pueden ser culpables.
Si un operador sospecha que un flujo deficiente está causando el problema, intente ajustar el medidor de flujo de gas para asegurarse de que la tasa sea adecuada. Cuando se utiliza un modo de transferencia por aspersión, por ejemplo, debería ser suficiente un flujo de 35 a 50 pies cúbicos por hora (cfh). Soldar a amperajes más altos requiere un aumento en el caudal, pero es importante no establecer el caudal demasiado alto. Esto puede provocar turbulencias en algunos diseños de armas que interrumpan la cobertura del gas protector.
Es importante tener en cuenta que las pistolas con diseños diferentes tienen diferentes características de flujo de gas (consulte los dos ejemplos a continuación). El "punto óptimo" del caudal de gas para el diseño superior es mucho mayor que el del diseño inferior. Esto es algo que un ingeniero de soldadura debe considerar al configurar la celda de soldadura.
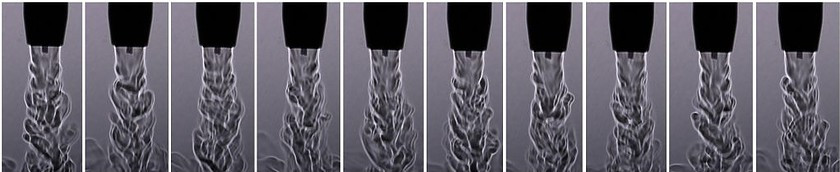
El diseño 1 muestra un flujo de gas suave en la salida de la boquilla.
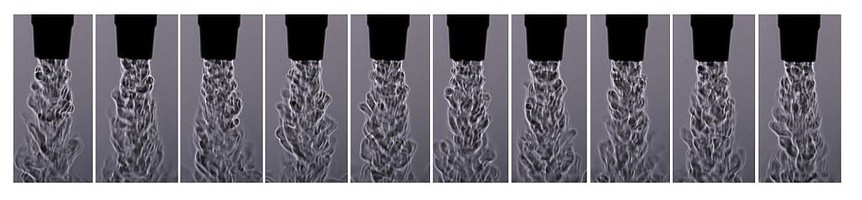
El diseño 2 muestra un flujo de gas turbulento en la salida de la boquilla.
También verifique si hay daños en la manguera de gas, los accesorios y conectores, así como en las juntas tóricas en la clavija de alimentación de la pistola de soldar MIG. Reemplace según sea necesario.
Cuando utilice ventiladores para enfriar operadores o piezas en una celda de soldadura, tenga cuidado de que no apunten directamente al área de soldadura, donde podrían alterar la cobertura de gas. Coloque una pantalla en la celda de soldadura para protegerla del flujo de aire externo.
Vuelva a tocar el programa en aplicaciones robóticas para asegurarse de que haya una distancia adecuada entre la punta y el trabajo, que generalmente es de ½ a 3/4 de pulgada, dependiendo de la longitud deseada del arco.
Por último, reduzca las velocidades de desplazamiento si la porosidad persiste o consulte a un proveedor de pistolas MIG para obtener diferentes componentes frontales con mejor cobertura de gas.
Contaminación por metales comunes
La contaminación por metales básicos es otra razón por la que se produce la porosidad: desde aceite y grasa hasta cascarilla de laminación y óxido. La humedad también puede favorecer esta discontinuidad, especialmente en la soldadura de aluminio. Estos tipos de contaminantes suelen provocar una porosidad externa que es visible para el operador. El acero galvanizado es más propenso a la porosidad del subsuelo.
Para combatir la porosidad externa, asegúrese de limpiar minuciosamente el material base antes de soldar y considere utilizar un alambre de soldadura con núcleo metálico. Este tipo de alambre tiene niveles más altos de desoxidantes que el alambre sólido, por lo que es más tolerante a cualquier contaminante restante en el material base. Guarde siempre estos y otros cables en un área limpia y seca a una temperatura similar o ligeramente superior a la de la planta. Hacer esto ayudará a minimizar la condensación que podría introducir humedad en el baño de soldadura y causar porosidad. No almacene cables en un almacén frío o al aire libre.
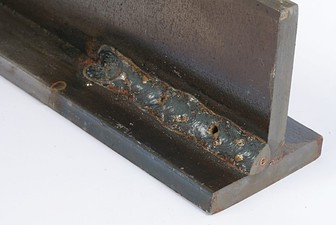
La porosidad, discontinuidades de tipo cavidad formadas por el atrapamiento de gas durante la solidificación, es un defecto común pero engorroso en la soldadura MIG y tiene varias causas.
Al soldar acero galvanizado, el zinc se vaporiza a una temperatura más baja que la que el acero se funde, y las velocidades de desplazamiento rápidas tienden a hacer que el baño de soldadura se congele rápidamente. Esto puede atrapar vapor de zinc en el acero, provocando porosidad. Combata esta situación controlando las velocidades de desplazamiento. Nuevamente, considere un alambre con núcleo metálico especialmente diseñado (fórmula fundente) que promueve el escape del vapor de zinc del baño de soldadura.
Boquillas obstruidas y/o de tamaño insuficiente
Las boquillas obstruidas y/o de tamaño insuficiente también pueden causar porosidad. Las salpicaduras de soldadura pueden acumularse en la boquilla y en la superficie de la punta de contacto y el difusor, lo que puede restringir el flujo del gas de protección o provocar que se vuelva turbulento. Ambas situaciones dejan el baño de soldadura con una protección inadecuada.
Para agravar esta situación hay una boquilla que es demasiado pequeña para la aplicación y más propensa a una acumulación de salpicaduras mayor y más rápida. Las boquillas más pequeñas pueden proporcionar un mejor acceso a las juntas, pero también obstruir el flujo de gas debido al área de sección transversal más pequeña permitida para el flujo de gas. Tenga siempre en cuenta la variable de la punta de contacto con el saliente (o hueco) de la boquilla, ya que este puede ser otro factor que afecte el flujo del gas de protección y la porosidad con su selección de boquilla.
Teniendo esto en cuenta, asegúrese de que la boquilla sea lo suficientemente grande para la aplicación. Normalmente, las aplicaciones con alta corriente de soldadura que utilizan tamaños de alambre más grandes requieren una boquilla con tamaños de orificio más grandes.
En aplicaciones de soldadura semiautomática, verifique periódicamente si hay salpicaduras de soldadura en la boquilla y retírelas con unos alicates de soldador (welpers) o reemplace la boquilla si es necesario. Durante esta inspección, confirme que la punta de contacto esté en buen estado y que el difusor de gas tenga puertos de gas transparentes. Los operadores también pueden usar un compuesto antisalpicaduras, pero deben tener cuidado de no sumergir la boquilla en el compuesto demasiado o durante demasiado tiempo, ya que cantidades excesivas del compuesto pueden contaminar el gas protector y dañar el aislamiento de la boquilla.
En una operación de soldadura robótica, invierta en una estación de limpieza de boquillas o en un escariador para combatir la acumulación de salpicaduras. Este periférico limpia la boquilla y el difusor durante las pausas rutinarias de la producción para que no afecte el tiempo del ciclo. Las estaciones de limpieza de boquillas están diseñadas para funcionar en conjunto con un rociador antisalpicaduras, que aplica una fina capa del compuesto a los componentes frontales. Demasiado o muy poco líquido antisalpicaduras puede provocar una porosidad adicional. Agregar un chorro de aire al proceso de limpieza de boquillas también puede ayudar a eliminar las salpicaduras sueltas de los consumibles.
Mantener la calidad y la productividad.
Si se tiene cuidado de controlar el proceso de soldadura y se conocen las causas de la porosidad, es relativamente sencillo implementar soluciones. Hacerlo puede ayudar a garantizar un mayor tiempo de encendido del arco, resultados de calidad y más piezas buenas en movimiento durante la producción.
Hora de publicación: 02-feb-2020