En muchos casos, los consumibles de las pistolas MIG pueden ser una ocurrencia tardía en el proceso de soldadura, ya que las preocupaciones con el equipo, el flujo de trabajo, el diseño de piezas y más dominan la atención de los operadores de soldadura, los supervisores y otras personas involucradas en la operación. Sin embargo, estos componentes, en particular las puntas de contacto, pueden tener un impacto significativo en el rendimiento de la soldadura.
En un proceso de soldadura MIG, la punta de contacto es responsable de transferir la corriente de soldadura al alambre a medida que pasa a través del orificio, creando el arco. De manera óptima, el cable debe pasar con una resistencia mínima y al mismo tiempo mantener el contacto eléctrico. Igualmente importante es la posición de la punta de contacto dentro de la boquilla, denominada rebaje de la punta de contacto. Puede influir en la calidad, la productividad y los costes en la operación de soldadura. También puede afectar la cantidad de tiempo dedicado a realizar actividades sin valor agregado, como moler o volar piezas que no contribuyen al rendimiento o rentabilidad general de la operación.
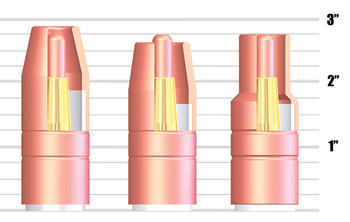
El hueco correcto de la punta de contacto varía según la aplicación. Debido a que una menor extensión del cable generalmente resulta en un arco más estable y una mejor penetración de bajo voltaje, la mejor longitud de extensión del cable es generalmente la más corta permitida para la aplicación.
El impacto en la calidad de la soldadura.
El receso de la punta de contacto afecta una serie de factores que a su vez pueden influir en la calidad de la soldadura. Por ejemplo, la extensión del electrodo o saliente (la longitud del cable entre el extremo de la punta de contacto y la superficie de trabajo) varía según el hueco de la punta de contacto; específicamente, cuanto mayor sea el hueco de la punta de contacto, más largo será el saliente del cable. A medida que aumenta la extensión del cable, el voltaje aumenta y el amperaje disminuye. Cuando esto ocurre, el arco puede desestabilizarse, provocando salpicaduras excesivas, oscilaciones del arco, control deficiente del calor en metales delgados y velocidades de desplazamiento más lentas.
El hueco de la punta de contacto también afecta el calor radiante del arco de soldadura. La acumulación de calor provoca un aumento de la resistencia eléctrica en los consumibles frontales, lo que reduce la capacidad de la punta de contacto para pasar la corriente al cable. Esta mala conductividad puede provocar una penetración insuficiente, salpicaduras y otros problemas que podrían dar como resultado una soldadura inaceptable o llevar a un retrabajo.
Además, demasiado calor generalmente reduce la vida útil de la punta de contacto. El resultado son mayores costos generales de consumibles y un mayor tiempo de inactividad para el cambio de puntas de contacto. Debido a que la mano de obra es casi siempre el mayor costo en una operación de soldadura, ese tiempo de inactividad puede generar aumentos innecesarios en los costos de producción.
Otro factor importante afectado por el hueco de la punta de contacto es la cobertura del gas protector. Cuando el hueco de la punta de contacto coloca la boquilla más lejos del arco y del charco de soldadura, el área de soldadura es más susceptible al flujo de aire que puede perturbar o desplazar el gas protector. Una mala cobertura del gas de protección provoca porosidad, salpicaduras y una penetración insuficiente.
Por todas estas razones, es importante utilizar el hueco de contacto correcto para la aplicación. A continuación se presentan algunas recomendaciones.
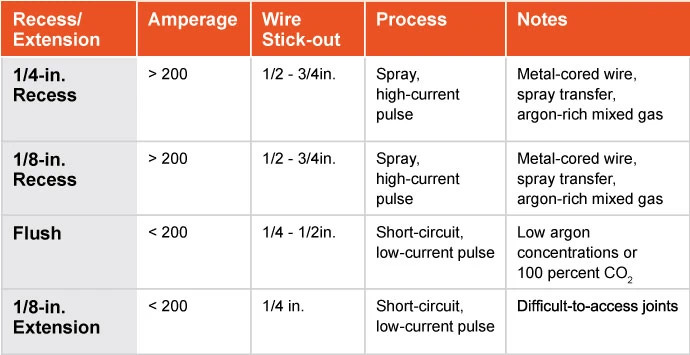
Figura 1: El hueco correcto de la punta de contacto varía según la aplicación. Consulte siempre las recomendaciones del fabricante para determinar el hueco de la punta de contacto adecuado para el trabajo.
Tipos de receso para punta de contacto
El difusor, la punta y la boquilla son las tres partes principales que componen los consumibles de la pistola MIG. El difusor se conecta directamente al cuello de la pistola, transporta corriente hasta la punta de contacto y dirige el gas hacia la boquilla. La punta se conecta con el difusor y transfiere la corriente al cable mientras lo guía a través de la boquilla y hacia el charco de soldadura. La boquilla se conecta al difusor y sirve para mantener el gas protector enfocado en el arco de soldadura y el charco. Cada componente juega un papel fundamental en la calidad general de la soldadura.
Hay dos tipos de receso para punta de contacto disponibles con los consumibles de la pistola MIG: fijo o ajustable. Debido a que un hueco de punta de contacto ajustable se puede cambiar a diferentes rangos de profundidad y extensiones, tienen la ventaja de poder satisfacer las demandas de hueco de diferentes aplicaciones y procesos. Sin embargo, también aumentan el potencial de error humano, ya que los operadores de soldadura los ajustan maniobrando la posición de la boquilla o mediante un mecanismo de bloqueo que asegura la punta de contacto en un hueco determinado.
Para evitar variaciones, algunas empresas prefieren puntas con ranura fija como forma de garantizar la uniformidad de la soldadura y lograr resultados consistentes de un operador de soldadura a otro. Las puntas con huecos fijos son comunes en aplicaciones de soldadura automatizada donde una ubicación constante de la punta es fundamental.
Diferentes fabricantes fabrican consumibles que se adaptan a una variedad de profundidades de huecos para puntas de contacto, que normalmente varían desde un hueco de 1⁄4 de pulgada hasta una extensión de 1⁄8 de pulgada.
Determinar el receso correcto
El hueco correcto de la punta de contacto varía según la aplicación. Una buena regla a considerar es que, en la mayoría de las condiciones, a medida que aumenta la corriente, el receso también debería aumentar. Además, debido a que una menor extensión del cable generalmente resulta en un arco más estable y una mejor penetración de bajo voltaje, la mejor longitud de extensión del cable es generalmente la más corta permitida para la aplicación. Aquí hay algunas pautas a continuación. Consulte también la Figura 1 para obtener notas adicionales.
1. Para soldadura pulsada, procesos de transferencia por pulverización y otras aplicaciones de más de 200 amperios, se recomienda un hueco para la punta de contacto de 1/8 de pulgada o 1/4 de pulgada.
2. Para aplicaciones con corrientes más altas, como aquellas que unen metales gruesos con alambre de gran diámetro o alambre con núcleo metálico con un proceso de transferencia por pulverización, una punta de contacto empotrada también puede ayudar a mantener la punta de contacto alejada del alto calor del arco. El uso de un cable saliente más largo para estos procesos ayuda a reducir la aparición de quemaduras (donde el cable se funde y se atasca en la punta de contacto) y salpicaduras, lo que ayuda a extender la vida útil de la punta de contacto y reducir los costos de consumibles.
3. Cuando se utiliza un proceso de transferencia de cortocircuito o soldadura por pulsos de baja corriente, generalmente se recomienda una punta de contacto al ras con un cable que sobresalga de aproximadamente 1⁄4 de pulgada. La longitud relativamente corta del saliente permite la transferencia de cortocircuito para soldar materiales delgados sin riesgo de quemaduras o deformaciones y con pocas salpicaduras.
4. Las puntas de contacto extendidas generalmente se reservan para un número muy limitado de aplicaciones de cortocircuito con configuraciones de juntas de difícil acceso, como juntas con ranura en V profundas y estrechas en soldadura de tuberías.
Estas consideraciones pueden ayudar con la elección, pero siempre consulte las recomendaciones del fabricante para determinar el hueco de la punta de contacto adecuado para el trabajo. Recuerde, la posición correcta puede reducir la posibilidad de que se produzcan salpicaduras excesivas, porosidad, penetración insuficiente, quemaduras o deformaciones en materiales más delgados, etc. Además, cuando una empresa reconoce que el receso de la punta de contacto es el culpable de tales problemas, puede ayudar a eliminar la solución de problemas costosa y que requiere mucho tiempo o las actividades posteriores a la soldadura, como el retrabajo.
Información adicional: Seleccione consejos de calidad
Debido a que las puntas de contacto son un factor importante para completar soldaduras de calidad y reducir el tiempo de inactividad, es importante seleccionar una punta de contacto de alta calidad. Si bien estos productos pueden costar un poco más que los productos de menor calidad, ofrecen valor a largo plazo al extender la vida útil y reducir el tiempo de inactividad para el cambio. Además, se pueden fabricar puntas de contacto de mayor calidad a partir de aleaciones de cobre mejoradas y, por lo general, se mecanizan con tolerancias mecánicas más estrictas, lo que crea una mejor conexión térmica y eléctrica para minimizar la acumulación de calor y la resistencia eléctrica. Los consumibles de mayor calidad suelen tener un orificio central más liso, lo que genera menos fricción a medida que pasa el alambre. Eso significa una alimentación de alambre consistente con menos resistencia y menos problemas potenciales de calidad. Las puntas de contacto de mayor calidad también pueden ayudar a minimizar las quemaduras y ayudar a prevenir un arco errático causado por una conductividad eléctrica inconsistente.
Hora de publicación: 01-ene-2023