La soldadura de aleaciones de aluminio es muy diferente de la soldadura de acero al carbono en general, acero inoxidable y otros materiales. Es fácil producir muchos defectos que otros materiales no tienen y es necesario tomar medidas específicas para evitarlos. Echemos un vistazo a los problemas que ocurren fácilmente en la soldadura de aleaciones de aluminio y los requisitos de la tecnología de soldadura.
Dificultades para soldar materiales de aleación de aluminio La conductividad térmica de los materiales de aleación de aluminio es de 1 a 3 veces mayor que la del acero y es fácil de calentar. Sin embargo, este material no es resistente a las altas temperaturas y tiene un gran coeficiente de expansión cuando se calienta, lo que fácilmente provoca deformaciones por soldadura. Además, este material es propenso a agrietarse y a la penetración de la soldadura durante la soldadura, especialmente la soldadura de placas de aluminio delgadas es más difícil.
El equipo de soldadura Xinfa tiene las características de alta calidad y bajo precio. Para más detalles, visite:Fabricantes de soldadura y corte - Fábrica y proveedores de soldadura y corte de China (xinfatools.com)
La soldadura de aleaciones de aluminio producirá una cierta cantidad de hidrógeno en el baño fundido. Si estos gases no se descargan antes de que se forme la soldadura, se producirán poros en la soldadura y afectarán la calidad de las piezas soldadas.
El aluminio es un metal que se oxida fácilmente y casi no hay aluminio sin oxidar en el aire. Cuando la superficie de la aleación de aluminio se expone directamente al aire, se formará en su superficie una película densa e insoluble de óxido de aluminio. La película de óxido es extremadamente resistente al desgaste y a las altas temperaturas, con un punto de fusión de más de 2000 grados Celsius. Una vez formado, la dificultad de procesamiento posterior aumentará considerablemente.
La soldadura de aleaciones de aluminio también tiene problemas, como que la junta se ablanda fácilmente y la tensión superficial en estado fundido es pequeña y es fácil producir defectos.
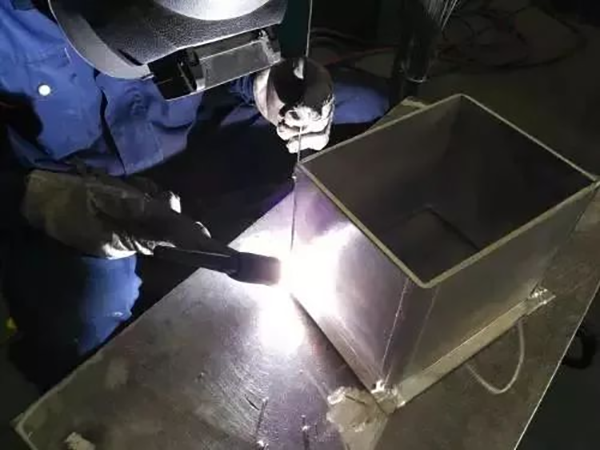
Requisitos para el proceso de soldadura de aleaciones de aluminio.
En primer lugar, desde la perspectiva del equipo de soldadura, si se utiliza una máquina de soldar MIG/MAG, esta debe tener funciones de pulso como pulso simple o pulso doble. La función de doble pulso tiene el mejor efecto. El pulso doble es la superposición de un pulso de alta frecuencia y un pulso de baja frecuencia, y el pulso de baja frecuencia se utiliza para modular el pulso de alta frecuencia. De esta manera, la corriente de doble pulso se fija en la frecuencia del pulso de baja frecuencia para cambiar periódicamente entre la corriente máxima y la corriente base, de modo que la soldadura forme escamas de pescado regulares.
Si desea cambiar el efecto de formación de la soldadura, puede ajustar la frecuencia y el valor máximo del pulso de baja frecuencia. El ajuste de la frecuencia del pulso de baja frecuencia afectará la velocidad de conmutación entre el valor máximo y el valor base de la corriente de doble pulso, lo que cambiará el espaciado del patrón de escamas de pescado de la soldadura. Cuanto mayor sea la velocidad de conmutación, menor será el espaciado del patrón de escamas de pescado. Ajustar el valor máximo del pulso de baja frecuencia puede cambiar el efecto de agitación en el baño fundido, cambiando así la profundidad de soldadura. La elección de un valor máximo adecuado tiene efectos obvios en la reducción de la generación de poros, la reducción del aporte de calor, la prevención de la expansión y la deformación y la mejora de la resistencia de la soldadura.
Además, desde la perspectiva del proceso de soldadura, cabe señalar las siguientes cuestiones:
Primero, se debe limpiar la superficie de la aleación de aluminio antes de soldar y se debe eliminar todo el polvo y el aceite. Se puede utilizar acetona para limpiar la superficie del punto de soldadura de aleación de aluminio. Para placas de aleación de aluminio gruesas, se debe limpiar primero con un cepillo de alambre y luego con acetona.
En segundo lugar, el material del alambre de soldadura utilizado debe ser lo más parecido posible al material original. La elección de alambre de soldadura de silicio de aluminio o alambre de soldadura de magnesio de aluminio debe determinarse de acuerdo con los requisitos de la soldadura. Además, el alambre de soldadura de aluminio y magnesio solo se puede usar para soldar materiales de aluminio y magnesio, mientras que el alambre de soldadura de aluminio y silicio se usa relativamente más ampliamente. Puede soldar materiales de aluminio, silicio y materiales de aluminio y magnesio.
En tercer lugar, cuando el espesor de la placa es grande, la placa debe precalentarse con anticipación; de lo contrario, será fácil soldarla. Al cerrar el arco, se debe utilizar una pequeña corriente para cerrar el arco y llenar el pozo.
En cuarto lugar, al realizar soldadura por arco de gas inerte de tungsteno, se debe usar una máquina de soldadura por arco de argón de CC, y se debe usar CA y CC hacia adelante y hacia atrás alternativamente. La CC directa se utiliza para limpiar el molde de oxidación de la superficie de los materiales de aluminio y la CC inversa se utiliza para soldar.
También tenga en cuenta que las especificaciones de soldadura deben establecerse de acuerdo con el espesor de la placa y los requisitos de soldadura; La soldadura MIG debe utilizar una rueda de alimentación de alambre de aluminio especial y un tubo guía de alambre de teflón; de lo contrario, se generarán virutas de aluminio; El cable de la pistola de soldar no debe ser demasiado largo, ya que el alambre de soldadura de aluminio es blando y un cable de la pistola de soldar demasiado largo afectará la estabilidad de la alimentación del alambre.
Hora de publicación: 27 de agosto de 2024